Anti-Foam Control Solutions-- Trustworthy Foam Control for Chemical Processing
Anti-Foam Control Solutions-- Trustworthy Foam Control for Chemical Processing
Blog Article
How Anti-Foam Control Solutions Enhance Item High Quality and Efficiency
The duty of anti-foam control services in commercial processes can not be overemphasized, as they are critical in enhancing both item high quality and functional effectiveness. By successfully mitigating foam development, these solutions not just make certain regular item structure throughout numerous sectors but likewise decrease the threat of contamination, which is essential for preserving high pureness criteria. Moreover, their effect on improving procedures and decreasing downtime raises crucial questions regarding the option and application of these representatives. What specific variables should be considered when picking the right anti-foam option for your distinct operational requirements?
Recognizing Foam Formation
Foam formation is an usual sensation come across in different industrial processes, often arising from the interaction of liquids with gases or solids. This sensation happens because of the stablizing of gas bubbles within a liquid matrix, leading to the creation of a foamy layer externally. The existence of surfactants, which reduce the surface area tension of liquids, can exacerbate foam development by promoting bubble development and stabilization.
Several variables affect foam growth, including the nature of the liquid, the visibility of pollutants, temperature, and anxiety levels. For circumstances, high shear pressures during blending can introduce extra air right into the liquid, advertising bubble formation. In addition, hydrophobic and hydrophilic compounds can interact with fluid surfaces, impacting bubble stability.
Comprehending the mechanisms of foam formation is vital for markets such as food processing, pharmaceuticals, and petrochemicals, where foam can prevent production performance and alter item top quality. Recognizing the certain problems that result in foam generation enables better style and control of processes, eventually bring about enhanced functional end results. Acknowledging these basic aspects of foam formation establishes the stage for checking out reliable solutions to reduce its damaging results in industrial applications.

Value of Anti-Foam Solutions
While foam formation can boost specific processes, its unintended existence usually leads to considerable functional obstacles across different sectors. In manufacturing, for instance, too much foam can hinder the precise dimension of fluids, leading to inconsistencies in product formula.
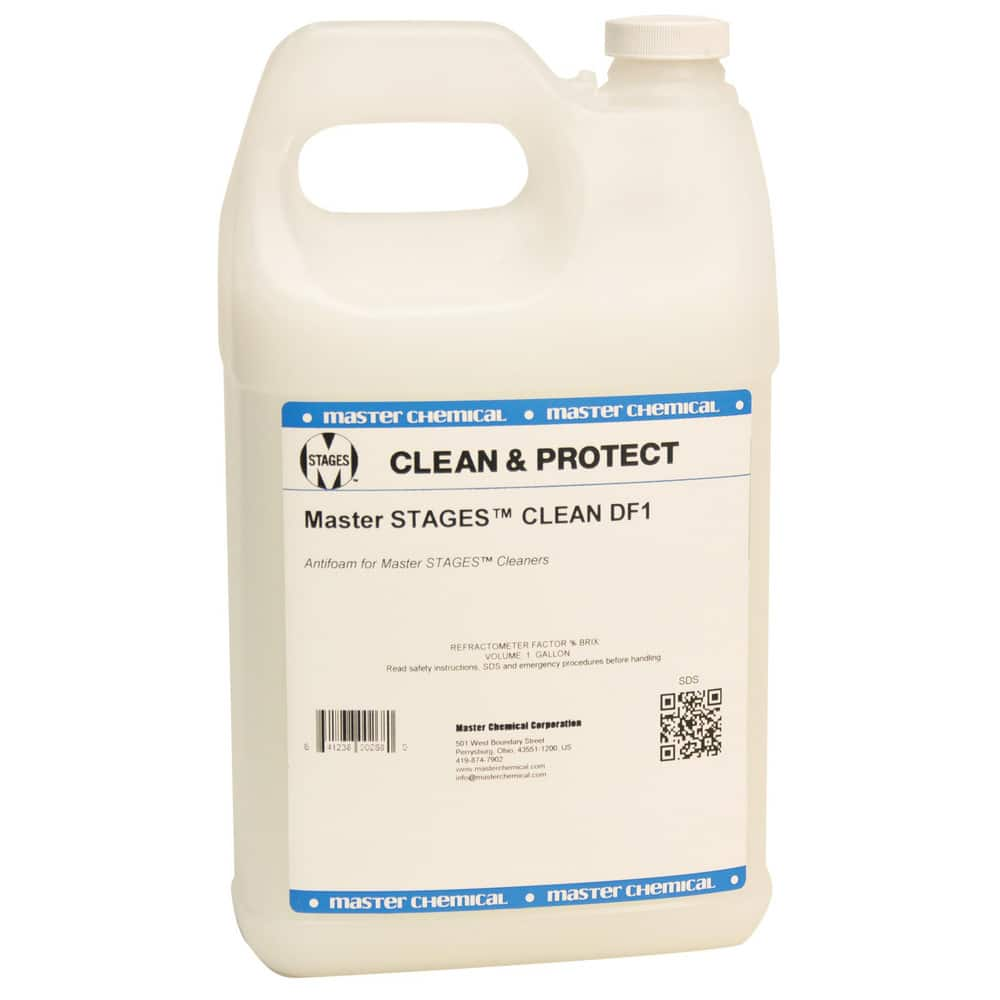
The importance of anti-foam options expands beyond operational performance; they also play an essential role in preserving safety and security standards. In markets such as food and drink handling, where health is critical, managing foam can protect against contamination risks connected with overflow and splilling. Inevitably, the implementation of anti-foam services is necessary for maximizing manufacturing processes, securing devices, and making certain conformity with industry regulations. Their function is vital in advertising total functional quality across diverse sectors.
Advantages to Item Top Quality
Reliable anti-foam options significantly enhance product top quality throughout numerous markets by making sure constant formulation and preventing the introduction of impurities. The presence of foam throughout production processes can lead to irregularity in product qualities, which ultimately affects completion individual's experience. By reducing foam formation, these remedies assist in uniform blending and diffusion of ingredients, resulting in an item that satisfies stringent top quality criteria.
In click this site addition, anti-foam representatives assist maintain optimum viscosity and texture, which are critical for products such as coatings, food, and drugs. Anti-Foam Control Solutions. A stable formulation is not just aesthetically enticing however additionally functionally remarkable, ensuring that items perform as planned. Additionally, the reduction of foam decreases the danger of contamination, as entraped air can introduce undesirable microorganisms or foreign fragments that jeopardize item integrity
In applications like fermentation or chain reaction, effective anti-foam options support ideal return and product consistency, which are crucial for preserving brand online reputation and customer fulfillment. By focusing on product high quality, suppliers can foster depend on and commitment among customers, ultimately adding to lasting success in the marketplace.
Enhancing Operational Effectiveness
A substantial reduction in foam can result in improved operational performance in making processes across different markets. When foam is decreased, it allows for smoother operations, thus minimizing downtime related to foam-related problems. Too much foam can create overflow, interrupt equipment functionality, and necessitate regular maintenance treatments, every one of which add to inefficiencies and enhanced operational costs.
By carrying out effective anti-foam control options, makers can streamline their processes, causing enhanced throughput and performance. The reduction of foam assists in far better mixing and response times in chemical procedures, which is essential in markets such as food manufacturing, drugs, and wastewater treatment. Moreover, with a more steady procedure setting, manufacturers can accomplish a lot more consistent product outcome, therefore enhancing overall operational integrity.
Additionally, improved operational effectiveness can cause financial savings in resources and power intake. When foam is controlled effectively, sources are made use of better, leading to a reduction in waste and operational costs. Consequently, organizations are better positioned to meet production targets and reply to market demands quickly, eventually adding to a stronger competitive advantage in the marketplace.
Picking the Right Anti-Foam Representative
Selecting the suitable anti-foam representative is essential for maintaining the operational efficiency gained via reliable foam control. The option of agent can significantly influence both the efficiency of the process and the my latest blog post quality of the last item. Elements such as the nature of the foam, the processing setting, and the certain application needs to be taken into consideration to make certain optimum results.
Anti-foam agents can be classified into 2 main types: non-silicone-based and silicone-based. Silicone agents are known for their premium efficiency in high-temperature and high-shear applications, while non-silicone representatives may be favored in markets like food and drink due to governing factors to consider. It is important to evaluate the compatibility of the anti-foam representative with the processes and materials entailed.
Furthermore, the focus of the anti-foam agent plays an essential role; too much use can cause negative influences on product high quality, while not enough amounts might stop working to regulate foam sufficiently. Performing extensive screening and pilot trials can assist recognize the most appropriate anti-foam agent for a particular application, inevitably improving both product high quality and functional performance.
Final Thought
In verdict, anti-foam control remedies play an essential duty in boosting item top quality and functional effectiveness throughout various industries. By minimizing foam formation, these solutions ensure consistent blending and item structure while alleviating contamination dangers.
By efficiently mitigating foam formation, these solutions not only make certain regular item appearance throughout different sectors but additionally lessen the danger of contamination, which is vital for maintaining high pureness requirements.Comprehending the devices of foam development is important for industries such as food handling, drugs, and petrochemicals, where foam can hinder manufacturing effectiveness and alter item high quality. The existence of foam during manufacturing processes can lead to variability in item qualities, which inevitably impacts the end user's experience. By minimizing foam formation, these solutions promote consistent mixing and diffusion of ingredients, resulting in an item that meets rigorous high quality criteria.
Choosing the ideal anti-foam representative is vital for maintaining the functional click effectiveness obtained with reliable foam control.
Report this page